Specific Lunac 2+ features:
- This hard crack free coating is highly resistant to adhesive and abrasive wear (adhesive wear test results: 23 N at 0.7 m/s; the combination Lunac 2+/Lunac 2+ is 19 times more wear resistant than the combination of hardened (HRc 64-66) DIN 1.2379 on hardened DIN 1.2379.
- Virtually immune to galling / fretting / cold welding or seizing problems in non-lubricated conditions.
Therefore this coating is ideal for heavily loaded and non-lubricated parts in relative motion. - Lunac 2+ duplex has proved to be one of the most reliable corrosion protection systems in (sea)water.
- Often, wear of the non-coated opposing part is also significantly reduced, especially in sea water.
- The coefficient of friction is 30% lower than that of hardened steel DIN 1.2379 on steel 1.2379.
- Steel cylinders and rods coated with Lunac 2+ are practically equal to HVOF
ceramic plated cylinders with respect to wear, but are much cheaper,
much less vulnerable and help prevent high seal wear. - Although moisture can slightly tarnish the Lunac 2+ surface,
Lunac 2+ coatings continue to be highly efficient. - Lunac 2+ resists oxidative wear (tribo wear) very well.
- Complies fully with the RoHS standard.
- Relatively ductile (elongation 0.28%).
General Lunac system features:
|
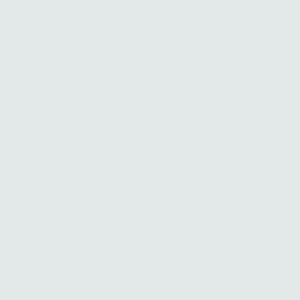
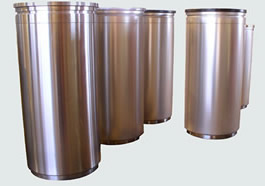
Figure 2. The main-bearing axles in the doors of the Kornwerderzand lock of the major northern Dutch IJsselmeer dam have been Lunac 2+ coated because of the corrosion resistance, abrasive (sand) wear resistance and shock resistance (waves) of the coating. Moreover the Lunac 2+ coefficient of friction in water contact conditions can be exceptionally low.
Figure 3. Heavy lifting hydraulic pistons coated with Lunac 2+. The most frequently received feedback relating to hydraulic equipment in harsh outdoor conditions is the long term reliability of the coating;
- high scratch resistance and no oil leakage
- little seal or guide-strip wear
- no rust formation (and no under corrosion)
- accidents do not initiate a peeling process
but are limited to localized deformations
Picture: Enerpac